Client
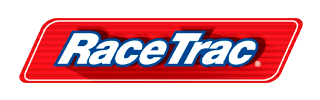
RaceTrac operates more than 600 stores in the southeast. They are known for their sprawling convenience store layouts. With 40 new stores and 100 remodels annually, RaceTrac selected ASD® to help them meet the rigorous scheduling needs with superior delivery of products and installation services.
Challenge
RaceTrac went through a period of rapid growth, but during this time some documentation and details fell through the cracks, most stores even lacked floor plans. With little information on layouts, infrastructure, and standards, it was difficult to develop an accurate scope of work.
IMPORTANT CONSIDERATIONS
- How do you bring on additional vendors with the lack of vendor documented processes?
- What’s the best way to develop joint labor & product standards that are economical, effective, and timely?
- What are the varying state-by-state regulations and needs?
![]() |
![]() |
|
Thanks for the consistent professionalism and effort on all projects this year. ASD® simply makes my job easier.
JIMMY
RaceTrac
Solution
To start, ASD® improved the product quality with the iCAT line of low-voltage products. They also became the subject matter experts from store installation to store opening, all at a consistent market price. ASD® worked in close collaboration with the general contractors and RaceTrac’s management/field PMs to learn, document, and deliver a store that met all construction milestones, implementation demands, and installation and support needs.
![]() |
Result
Thanks to the ASD® team, RaceTrac now has an organized and documented infrastructure. If they continue to expand or remodel in the future there are now detailed plans and standards. Their stores are safer, stylish, and up-to-date. Employees can easily communicate with customers who are at the pumps, communicate within the store, update menu displays, monitor fuel tank levels, and more.